The Critical Role of Accurate Wind Measurement for Wind Assisted Ship Propulsion
Insensys - WASP paper - Jan 2024
THE CRITICAL ROLE OF ACCURATE WIND MEASUREMENT FOR WIND ASSISTED SHIP PROPULSION January 2024
2
THE CRITICAL ROLE OF ACCURATE WIND MEASUREMENT FOR WIND ASSISTED SHIP PROPULSION CONTENTS Executive summary 4 - 5 Introduction 6 - 7 Wind measurement for Wind Assisted Ship Propulsion 8 - 11 Challenges of accurate wind sensing on board 13 Accurate 昀椀bre-optic wind sensing methods 14 - 17 Impact on ship performance 18 - 19 Bene昀椀ts of load & stress monitoring 20 Translating data into performance 23 About this white paper 25 3
THE CRITICAL ROLE OF ACCURATE WIND MEASUREMENT FOR WIND ASSISTED SHIP PROPULSION EXECUTIVE SUMMARY With the global imperative to decarbonise the shipping industry being an ever-growing priority for ship owners, operators and customers, the opportunity of utilising ocean winds as a free energy source for assisting ship propulsion cannot be ignored. A variety of Wind Assisted Ship Propulsion (“WASP”) technologies are being actively promoted for wider-scale market adoption such as 昀氀ettnor rotors, wing sails and suction sails. This white paper explores how the latest sensing systems, when used in conjunction with these WASP technologies can enhance performance and provide additional assurance around structural health, thereby making the business case for adoption of WASP technologies signi昀椀cantly more persuasive from both decarbonisation and cost reduction perspectives. This paper looks at a number of di昀昀erent types of sensing system including: Anemometers; LIDAR; Electrical resistive strain gauges; and Fibre-optic load sensors. It looks at both the challenges and bene昀椀ts of using the di昀昀erent sensing technologies. Those challenges include the interactions between adjacent and surrounding mechanical sail units, the deck structure and other housings; the impact of the incoming wind gradient speed, 昀氀ow vortices, turbulence due to wind gusts and water spray causing 昀氀ow disruptions and air density variations. These challenges can make some forms of sensing less e昀昀ective and negate some of the potential bene昀椀ts. We have summarised below the comparative performance of each of the sensing technologies when assessed against the following criteria: • Complexity of installation; • Calibration requirements; • Susceptibility to motions; • Total capex and lifecycle cost; and • Accuracy. ANEMOMETERS (page 8) LIDAR (page 9) Complexity of Installation Complexity of Installation Calibration requirements Calibration requirements Susceptibility to motions Susceptibility to motions Total life cycle cost Total life cycle cost Accuracy Accuracy STRAIN GAUGES (page 12) FIBRE-OPTICS (page 16) Complexity of Installation Complexity of Installation Calibration requirements Calibration requirements Susceptibility to motions Susceptibility to motions Total life cycle cost Total life cycle cost Accuracy Accuracy 4
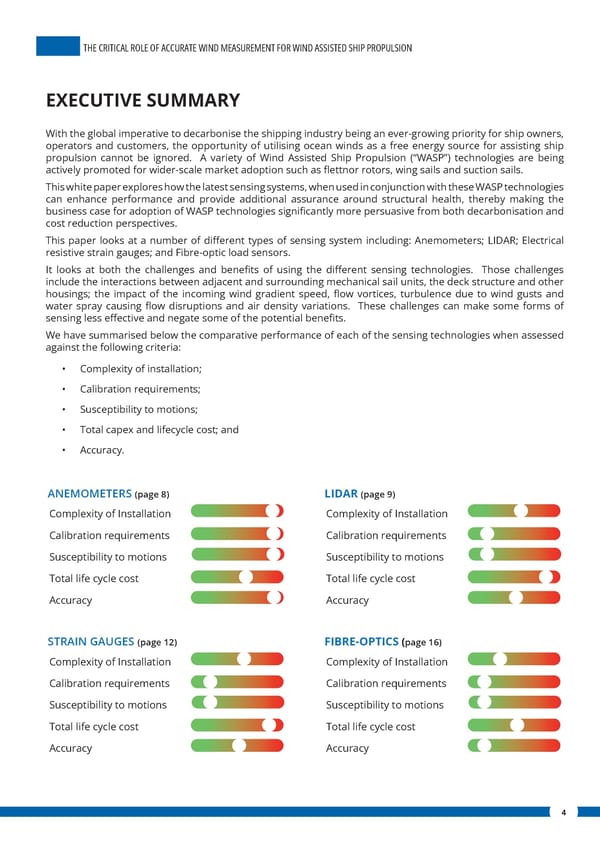
THE CRITICAL ROLE OF ACCURATE WIND MEASUREMENT FOR WIND ASSISTED SHIP PROPULSION The Insensys 昀椀bre-optic load monitoring system constantly provides real time thrust measurements for the WASP application. This data can be used locally for performance alerts, and logged for longer term analysis. THE POWER OF FIBRE-OPTICS OPTIMISE PERFORMANCE ENHANCE SAFETY REDUCE COSTS The analysis of alternative technologies show that there are clear advantages from installing 昀椀bre-optic sensors in WASP structures. Insensys are market leaders in this area with a 20-year proven track record in both the marine and wind energy industries of enabling wind capture optimisation. To illustrate the impact of adoption of accurate 昀椀bre-optic sensing for WASP, the estimated CO2 and fuel cost savings has been calculated for propulsion power without WASP, with WASP and with WASP 昀椀tted with Insensys 昀椀bre-optic load sensors. Propulsion M/E power (%) Fuel savings CO2 savings Total Voyage cost power (ton/hr) (tonCO2/hr) savings (USD/hr) Without WASP 100 - - - With WASP 49.12 0.605 1.936 617.1 With Insensys 642.6 昀椀tted WASP 47.1 0.630 2.016 (+4.13%) This 4.13% improvement in fuel performance could represent savings in excess of $100,000 per vessel per annum, making the payback period for installation of such a sensing system well within a year. Insensys systems are designed to operate in harsh marine conditions with little or no maintenance for 25 years, with a proven track record from installed systems dating back to 2006. Therefore, the fuel savings over the life-time of a vessel at current fuel prices are expected to be in the millions rather than thousands of US dollars. In addition, Insensys sensors can become a bene昀椀cial source of data for load and stress monitoring further optimising operability and prolonging the WASP system lifetime. On the basis of the above 昀椀ndings, Insensys 昀椀bre-optic load sensing systems are seen as an essential feature on all WASP applications. 5
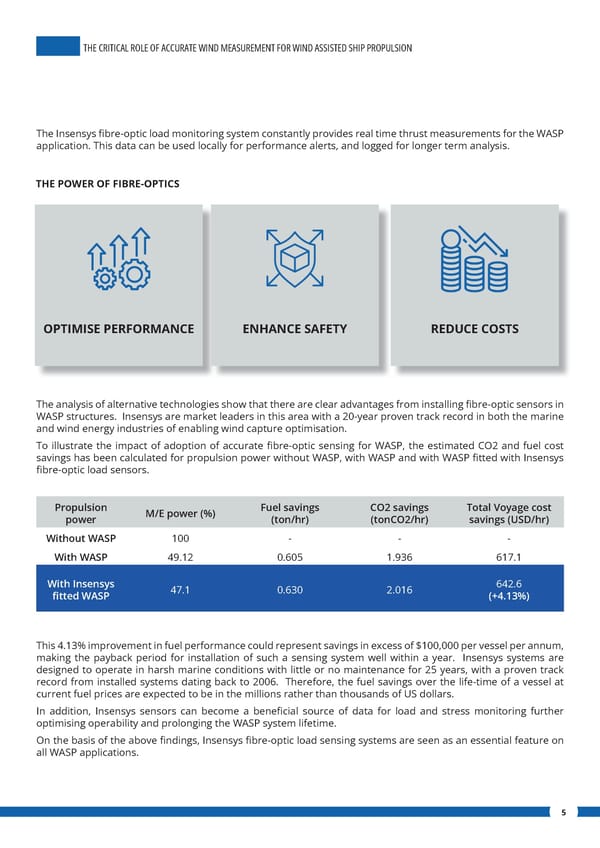
THE CRITICAL ROLE OF ACCURATE WIND MEASUREMENT FOR WIND ASSISTED SHIP PROPULSION INTRODUCTION The shipping industry has an environmental and commercial imperative to decarbonise. The regulatory framework developed by the IMO (International Maritime Ogranisation), the European Union and other Shipping Nations projects a gradual phase-out of GHG emissions from ships, with the IMO aiming at 70% reductions by 2050, while ongoing negotiations may bring a zero-emissions requirement by the same year. It is not only about imposing carbon levies to penalise polluter ship owners and operators: it is also about introducing carbon footprint per fuel energy spent (FuelEU Maritime[1]) and fuel lifecycle GHG intensity (IMO[2]), which will necessitate a large improvement of ship performance both by means of energy e昀케ciency and of low or zero carbon fuel/energy usage. The exploitation of Winds in the oceans for propulsion is an old concept, but still available as an abundant, inexhaustible source of energy with no price 昀氀uctuations. The traditional Sails that were once used for ship sailing and trading were comprised of large soft material surfaces which could be deployed when the wind was blowing, tightened, and twisted through ropes to develop a stable and e昀昀ective aerodynamic surface, with the mast turned to orientate appropriately with the incoming winds. This requires continuous human e昀昀ort and elaborative training for the decision making on the Sail adjustments and the assumptions around about the wind conditions surrounding the vessel. Modern ships though, having large displacements, are carrying relatively heavy cargo’s compared to the historical wind sailing ships, and require higher trading speeds, thus increased propulsion power, a combination of performance features which turned the shipping community to rather opt for more powerful internal combustion engines and mechanical propelling systems. Since the early years of the Millennium, a new breed of sailing systems for shipping were devised and developed for adoption and, with the primary aim to reduce high fuel costs for such high-power demand by improving energy e昀케ciency: the Mechanical Sails; Airborne Towing Kite during [3]; and the Flettner Rotor Sail[4]. MODERN SAIL OPTIONS Rotor Rigid wings Soft wings Soft Ventilated foil 70% BY 2050 6
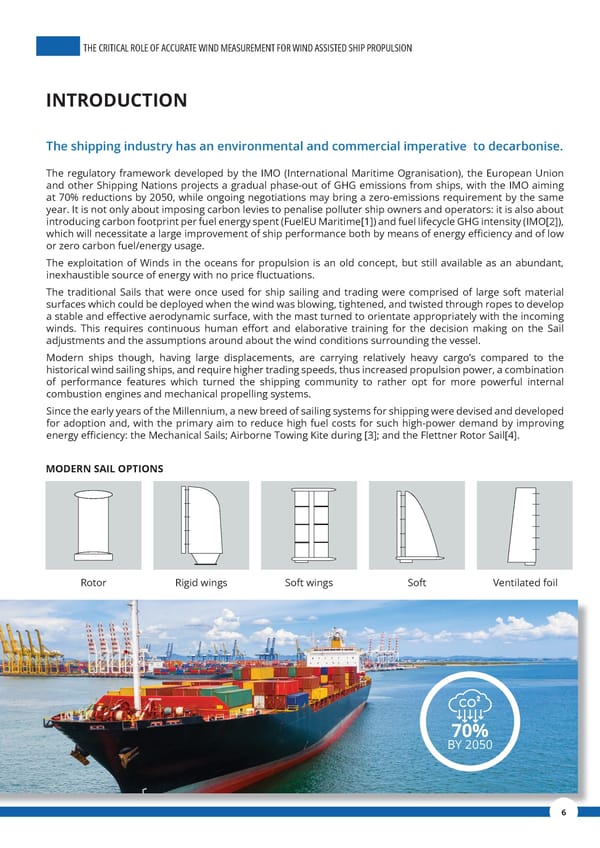
THE CRITICAL ROLE OF ACCURATE WIND MEASUREMENT FOR WIND ASSISTED SHIP PROPULSION Various types of mechanical sails for WASP - Rotor Sails (left), Wing Sails (right) Mechanical sails are currently used in wind prime applications, and wind for assisted propulsion both are devices which have been designed in such ways - and developed with such mechanical means - to automatically adjust their properties so that they maximise the delivered Thrust per square meter of Sail surface against the incoming winds, by arti昀椀cially elevating their aerodynamic properties, while working with the least human intervention, being semi or fully automated. In particular, the enhancement of aerodynamics is taking place through regulating the below parameters as applicable per di昀昀erent mechanical sail technology and type: • Rotor Sails: spinning RPM; • Suction Wing Sails: suction fan RPM, 昀氀ap positioning and Angel of Attack (AoA) orientation against the wind; • Wing Sails: 昀氀ap positioning and AoA orientation; and • Airborne Towing Kite: Height of 昀氀ight adjustment from the ship’s deck and positioning against the ship’s forward course. Mechanical Sails cannot automatically and e昀昀ectively adjust any of their functional parameters to deliver performance, without a means to accurately detect and interpret the current incoming apparent wind direction and wind speed on a moving ship. Therefore, a wind sensing system is probably the most important component of any given mechanical sail technology, no matter how advanced mechanics, software intelligence or other novel approach is incorporated to maximise performance. Without proper wind sensing, the performance is undermined and ultimately compromised. 7
THE CRITICAL ROLE OF ACCURATE WIND MEASUREMENT FOR WIND ASSISTED SHIP PROPULSION WIND MEASUREMENT FOR WIND ASSISTED SHIP PROPULSION Over the following pages we have analysed the potential bene昀椀ts and limitations of the sensing technologies available to the Wind Assisted ship propulsion (WASP) industry. ANEMOMETERS ANEMOMETERS Complexity of Installation Calibration requirements Susceptibility to motions Total life cycle cost Accuracy Since the very 昀椀rst system applications of wind energy harvesting from propulsion by the 昀椀rst entrants in the respective market, the primary input source for measuring incoming wind conditions to the system is the ship’s Anemometer. The Anemometer is usually installed above the Navigation bridge of a typical commercial cargo or passenger vessel, which lays in the air draft region of 35-54 meters high from the loaded waterline (depending on the ship size, depth and height of accommodation) and situated from minimum 20 meters up to maximum 200 meters from the most proximal Wind propulsion unit (Figure 3), depending on the ship’s length and size. To enhance the wind measuring input to a given WASP system of which the sail arrangement is distributed widely across the ship’s main deck (such as the one shown in Figure 3), a 2nd anemometer can be added closer to the farthest forward installed units, ideally of a better quality than the bridge anemometer installed by the Yard, sometimes including an additional GPS (named as ‘weather station’ by some technology providers). Figure 3: Typical Anemometer on the navigation bridge of an Oil Tanker, feeding wind data to four Rotor Sails installed in various deck locations[1], 昀椀gure taken from BlueWEEK WASP Mallorca event presentation by Finocean. 8
THE CRITICAL ROLE OF ACCURATE WIND MEASUREMENT FOR WIND ASSISTED SHIP PROPULSION WIND MEASUREMENT FOR WIND ASSISTED SHIP PROPULSION The anemometer is not only far located far from the actual incoming - dynamically changing - wind into each individual mechanical sail, but it is also sensing a relatively streamlined in昀氀ow being quite much further and higher from the superstructure and freeboard interface of the ship. nd Even a 2 anemometer installed closer to the forward systems cannot be physically positioned high enough, so it measures the incoming wind on the lower 1/3 of the mechanical sail, an area which is highly disturbed from the boundary layer e昀昀ect occurring due to the freeboard-forecastle surroundings and is more susceptible to the wind gradient (ground e昀昀ect), hence again measuring a rather fully disturbed incoming wind. The most usual Anemometers being installed in existing cargo ships built in Asian Yards are of mechanical type (i.e. such as vane anemometers) selected as such for cost saving reasons (since their prime purpose anyways is to measure a simple and generically prevailing wind dataset), hence susceptible to ship motions (due to inertia forces on the instrument’s mechanical parts) while needing frequent re-calibration, thus introducing measurement errors. For modern ship constructions, certain ship owners proactively request from Yards to install ultrasonic anemometers, which have better features, such as no angle limit within the 360º range, no start wind speed limit, no moving parts and longer service life while certain sensors can ensure low dispersion error of the measurements even under strong winds, making the output more stable. Despite the quality level of the anemometer, the greatest disadvantage comes from it’s installation location. An anemometer installed on top of the Bridge Deck is at a height ranging from 5-20 meters from the main deck where usually the mechanical sails are installed, fully susceptible to the superstructure wind 昀氀ow distortions and even from the mechanical sails generated 昀氀ow distortions. Hence, when the mechanical sails are activated and adjust their operational parameters (i.e. RPM, Angle of Attack, etc) on basis of the Anemometer signals (wind speed and direction), they are not corresponding to the true incoming ones on their surfaces, thus not always providing the best possible Net forward thrust force to the ship, which is the ultimate scope of the wind-assist ship propulsion application. LIDAR LIDAR Complexity of Installation Calibration requirements Susceptibility to motions Total life cycle cost Accuracy For even more accurate measurements 3D laser scanning techniques are proposed by using LIDAR (Light Detection and Ranging) technology, which can be used to complement or even replace the less accurate anemometer measurements. LIDAR is relatively small sized equipment which can be installed either in the fore part of the ship (forecastle) or on the Bridge top or sides. LIDAR emits a pulsed laser, the signal of which is scattered by the aerosol movements in the air environment above the sea due to the incoming wind, hence the measurement of aerosol speed determines the wind speed. LIDAR can also measure wind speed, direction, turbulence and shear – thus in principle it provides a measured representation of the incoming homogenous wind 昀氀ow to the ship coming through a distance of minimum 20 metres up to 700 metres from the measurement point. 9
THE CRITICAL ROLE OF ACCURATE WIND MEASUREMENT FOR WIND ASSISTED SHIP PROPULSION When an horizontal pro昀椀ling LIDAR is used to scan on the horizontal plane, for example placed in front of the sail arrangement (i.e. in the forecastle deck), it can provide more incoming wind properties that the anemometer and can depict the instantly incoming undisturbed 昀氀ow right before approaching the ship interface, hence a better anticipated apparent wind data compared to the anemometer which is susceptible to surrounding air 昀氀ow disturbances. There is also a vertical pro昀椀ling LIDAR that can measure the incoming wind at a height up to 300m from the laser emitting point, so theoretically it could be installed aside a mechanical sail to measure incoming wind to several planes vertical to the sails. When it comes to a LIDAR installation on a ship, for an accurate measurement the LIDAR system must be well- aligned with the ship’s horizontal and vertical axis, while an inclinometer is implemented inside the optical head of the LIDAR in order to facilitate this levelling and provide tilt and roll values during the system operation. LIDAR can measure consecutively radial wind speeds, but it does not reconstruct the wind in real time. Every 10 minutes, LIDAR provides a relative wind direction for each measurement range, hence potentially missing local wind gusts and turbulent 昀氀ow coming onto the mechanical sails. The horizontal plane scanning LIDAR usually has a range from 50 to 700 meters at a data sampling rate of 1 Hz and identi昀椀es better the incoming wind on the ship environment, but still cannot capture the local disturbances, turbulence and other dynamically induced wind 昀氀ows directly incoming to each mechanical sail, while even if a vertical plane LIDAR is installed, the measurements will be a昀昀ected by the blind zone occurring from the nearby mechanical sails or other proximal superstructures, such as deckhouses, vent masts, hose cranes, etc. There is also a vertical plane scanning LIDAR system which can measure the incoming wind on a height up to 300 meters, and theoretically it could be installed right next to each mechanical sail foundation level to measure the incoming wind twist and boundary layer e昀昀ect, however the technology works accurately only for homogenous wind conditions and the measurements will be a昀昀ected by the blind zone occurring from the nearby mechanical sails or other proximal superstructures, such as deckhouses, vent masts, hose cranes, etc. To counter this, the vertical plane LIDAR could instead incorporate 昀氀ow complexity recognition algorithms, however it is still very di昀케cult to accurately represent the surrounding ship superstructures and dynamic 昀氀ow impact on those. The performance of a LIDAR may be degraded during adverse weather conditions (i.e. intense rain, fog or high turbulent winds that excite strong/dense water mist formation), and at critical moments when real-time decisions need to be made regarding the mechanical operation of the sail. In that sense LIDAR is a very useful supportive enhancing wind data measurement which improves (or can even replace very e昀昀ectively) the Anemometer to provide clarity feedback on the wind’s directional and speed parameters before encountering the ship. However, mechanical sails need real-time wind measurements for optimal performance parameter setting. Figure 4: LIDAR wind measurements during real wind-assist operations on a cargo ship[5] 10
THE CRITICAL ROLE OF ACCURATE WIND MEASUREMENT FOR WIND ASSISTED SHIP PROPULSION ELECTRICAL RESISTIVE STRAIN GAUGES STRAIN GAUGES Complexity of Installation Calibration requirements Susceptibility to motions Total life cycle cost Accuracy A more localised approach for receiving direct thrust measurements of the wind propulsion unit is to install typical/electrical resistive strain gauges, either on the lower body of the mast or on the foundation structure. Strain gauges are sensors whose electrical resistance varies with the applied force (strain, tensile and compressive) thus it can be used to measure and analyse the forces and moments acting in all three axes (x, y, z) – either those coming from pressure, movements, heat and even structural changes to the material they are attached upon. When external forces are applied to a stationary object, stress and strain are the result, with stress de昀椀ned as the object’s internal resisting forces, and strain is de昀椀ned as the displacement and deformation that occur. In the very 昀椀rst recent mechanical sail applications for wind propulsion such simple mechanical type strain gauges were installed to measure the direct thrust development from the Sail and associate it with the incoming wind measurements, as validation of their performance[6], such as for example used in the ex- ‘MAERSK PELICAN’ Aframax Tanker installation during 2019, where two (2) Rotor Sails were 昀椀tted. The strain gauges were located on the foundation of the Rotor Sail, as it is the anticipated that the developed aerodynamic forces from the sail will be transferred to the supporting structure and then delivered through that to the ship’s structure. Alternatively, the industry-wide strain gauges can be used and have been actually installed in the very 昀椀rst mechanical sail applications due to their relatively low cost of manufacture and simple installation onto metallic surfaces. However, strain gauges are manufactured from metallic materials that do not possess desirable properties for repetitive, high strain loading, where degradation and fatigue can occur prematurely when subject to these conditions, making them unsuitable for use some applications. One of these applications is the Wind Energy market, previous testing shows that strain gauges fail at around the six-month mark, or at approximately 3,000 cycles of high strain loading, when installed in a turbine – hence it is expected that the dynamic fatigue and multiple loading environment on a ship at seas will provide even worse performance. Electrical strain gauge systems measure the change in resistance at each point and therefore require power supplied to all sensors. In certain applications, such as those working closely with volatile or 昀氀ammable materials, as for example on deck mounted mechanical sails of Oil/Product tankers and Gas carriers, this is certainly a safety concern. Another worrying issue is that electrical strain gauges are prone to becoming detached from the object’s surface, due to the installation issues experienced with many materials, and as a result, it is likely that the strain gauge produces inaccurate data, as the strain transfer between the materials is weakened. There are also other issues related to strain gauges’ operational and measurement reliability especially when considering frequent calibration needs, being susceptible to electromagnetic interference, humidity, creep and fatigue, factors which render their long-term reliability unsuitable for mechanical sails. 11
THE CRITICAL ROLE OF ACCURATE WIND MEASUREMENT FOR WIND ASSISTED SHIP PROPULSION 12
THE CRITICAL ROLE OF ACCURATE WIND MEASUREMENT FOR WIND ASSISTED SHIP PROPULSION [7] CHALLENGES OF ACCURATE WIND MEASUREMENT ON BOARD Any deck mounted and deck operating wind propulsion technology is operating within a dynamic environment, where the incoming wind 昀椀eld is not homogenous and stable. The incoming wind properties (direction, intensity and 昀氀ow vectors) onto each mechanical sail are primarily a昀昀ected by: • Interaction e昀昀ects between adjacent and surrounding mechanical sail units; • Interaction e昀昀ects between each mechanical sail and the deck structure/superstructures (i.e. deck housings, hatch coamings, mechanical sail foundations, etc); • Interaction e昀昀ects to the mechanical sail due to the ship’s freeboard (distance of main deck level from waterline level); • The impact the incoming wind gradient (speed and direction varying from the sea level up to the maximum installation height of each mechanical sail); • Flow vortices around the ship deck, superstructures and mechanical sails tip vortices; • Turbulence and dynamic forces due to wind gusts; and • Water spray (green seas) causing 昀氀ow disruptions and air density variations. Mechanical Sails performance calculations and full scale tests (either numerical or physical) relate to a stable moving ship at sea, through calm waters and no winds, which is not the case when the ship usually encounters sea waves, currents, swell and wind-induced waves, hence experiencing roll, pitch, sway and heave motions while the wind is incoming in such heterogenous state already on to the mechanical sails. The meaningful apparent wind conditions for mechanical sails to generate net forward thrust on the ship are occurring for BF > 3, and by large probability extend (over 70%) at an apparent wind window of 0o – 90o, hence most of the time the ship will also experience close-haul to beamy waves, of various wave height, thus almost aways in a combined rolling and pitching state. Thus, mechanical sails will always work in a continuously changing Apparent Wind incoming 昀椀eld, which cannot be captured e昀昀ectively by an Anemometer or a LIDAR, as neither can measure the exact proximity of incoming wind conditions to the mechanical sail across its full height in real time. When wind propulsion technology providers develop estimations and numerical assessments for the aerodynamic coe昀케cients of their mechanical sails (such as the lift coe昀케cient CL, or drag coe昀케cient CD) they either use wind tunnel tests, CFD simulations, or stand- alone small of full-scale physical land tests, to derive their polar diagrams (i.e. the angular CL and CD performance of the mechanical sail at every incoming wind speed). Under all these methods the incoming wind 昀氀ow develops in a controlled environment or by isolating in昀氀uential parameters to reduce complexity. These Polar diagrams though (however re昀椀ned after physical tests) are used for performance predictions of mechanical sails that will work in dynamic environments, where the incoming wind 昀氀ow will be constantly changing over time, Thus the actual mechanical sail on board will deliver di昀昀erent thrust spectrum during every voyage. With local, direct, actual incoming wind 昀氀ow measurements across the full height of the mechanical sail, such information could feed di昀昀erently the operational parameters settings of mechanical sails (i.e. AoA, RPM, etc), so that they adjust to deliver the best possible net forward thrust force with the max possible tolerable side force to the ship, hence boosting performance for wind propulsion, matching more accurately performance expectations. Figure 5: Disturbed wind 昀氀ow on mechanical sails due to boundary layer in昀氀uences from the freeboard and superstructures (left) and due to interaction e昀昀ects between the sails (right) [7] 13
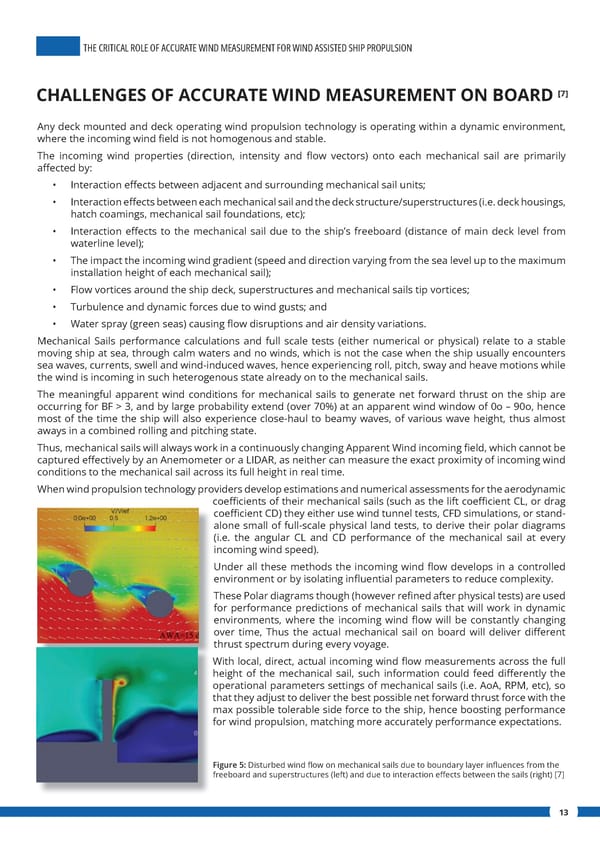
THE CRITICAL ROLE OF ACCURATE WIND MEASUREMENT FOR WIND ASSISTED SHIP PROPULSION ACCURATE FIBRE-OPTIC WIND SENSING METHODS FIBRE-OPTICS Complexity of Installation Calibration requirements Susceptibility to motions Total life cycle cost Accuracy Considering the above currently used options, the noticed limitations, restrictions and impact on delivering the maximum possible inherent performance capabilities of mechanical sails, Insensys 昀椀bre-optics sensors present a more reliable and enhanced alternative as a WASP wind and load sensing measurement solution. Fibre-optics sensors have long been used in land-based wind turbines, and have been proven very reliable, having as prime purpose to measure the wind turbine blade root bending moments for active control of wind turbine generators, by dynamically adjusting the pitch of each turbine blade in real time, thus increasing the wind turbine reliability and e昀케ciency. Insensys sensors are currently installed (with a reference base of > 7,000 systems) in composite 昀椀bre blades over 100 meters long, to continually measure the bending moment and loads at the root section of the blade where it connects to the rotor. Each blade load is balanced by making small pitch adjustments to each blade, enabling it to capture more or shed wind load accordingly. This enables the turbine to perform better (generating more electrical power), as well as reducing fatigue and maintenance on key drive train components. This application is called IPC (Individual Pitch Control). IPC delivers that extra 10% percent of turbine performance, similar to a turbo in a combustion engine. Equivalently, when a similar Insensys 昀椀bre-optics sensor system is used in mechanical sail applications for ship wind propulsion, they can provide multiple load point measurements, which can serve below purposes: • Depict at any given point of time the actual localised forces developed across the mechanical sail height (wind induced and ship induced), • Support accurate adjustments of the mechanical sail operating parameters (i.e. Angle of Attack, RPM, etc) for real-time optimal performance, • Compare with surrounding principal ship wind sensing system (i.e. anemometers and/or LIDAR), • Detect fatigue load limits and provide feedback on structural health of the mechanical sails, • Alert on-time for possible excess forces developed to the mechanical sail, undesired by means of ship safety. Insensys have proven wind load control systems for WASP technologies 昀椀rst trialled on DynaRig structures in 2002, which, similar to the IPC application for wind turbines, can provide advanced control loops to optimise their wind capture. Optical sensors embedded into the WASP structures can provide a real time control loop to adjust the structure, either in pitch, shape, or pro昀椀le. In a typical wind propulsion system arrangement (i.e. for a Wing Sail, Suction Wing, Rotor Sail, etc) a number of optical sensor arrays are installed in carefully selected locations usually where they experience a signi昀椀cant magnitude of strain signal, thus mostly near the bottom part of the Sail mast or tower and in other locations of critical importance, connected through Optical 昀椀bre Kevlar-reinforced cables to the Interrogator unit installed locally or remotely within the control panel of the wind propulsion system as seen in 昀椀gure 9. 14
THE CRITICAL ROLE OF ACCURATE WIND MEASUREMENT FOR WIND ASSISTED SHIP PROPULSION WASP control panel Interrogator unit Control loop Actuation Figure 9: Indicative arrangement of an Insensys 昀椀bre-optics sensor system on a mechanical sail (wing sail) 15
THE CRITICAL ROLE OF ACCURATE WIND MEASUREMENT FOR WIND ASSISTED SHIP PROPULSION Each Insensys sensor array contains 4 sensor patches, connected circumferentially via optical cables (Figure 6). Each sensor patch contains 2 Fibre Bragg Grating (FBG) sensors, 1 strain sensor and 1 temperature compensation sensor. The patch embedded 昀椀bre-optics sensors are making their installation onto other composite (as most current material that mechanical sail systems use for rotor sails, wing sails etc) or metallic surfaces a straightforward process, using specialist adhesives. Each sensor module contains a single continuous optical 昀椀bre as shown in 昀椀gure 7 which is embedded in ruggedised 昀椀breglass. The 4 modules together connect to form a single optical light path, while the connector box protects and rigidly holds the optical 昀椀bre in place. The interrogator contains a light source which pulses light through the optical cables to the FBG sensors. The wavelength of light re昀氀ected is dependent on the spacing of the gratings. Applying strain to the FBG sensor changes the spacing of the gratings and therefore changes the wavelength Figure 6: Sensor array of light re昀氀ected by the FBG (Figure 8). The wavelength of re昀氀ected light is proportional to the load experienced. All electronic components of the system, including the light source and detector, are housed in the interrogator unit. The interrogator unit processes the measurement data and transmits it to the wind propulsion unit’s PLC. The Fibre Sensor Interrogator sends optical signals to the sensors and measures the signal response from all FBG sensors installed on the mechanical sail. The signal response is then processed and communicated with each mechanical sail or wind propulsion central system PLC, over existing architecture of protocols (i.e. CAN bus, etc). Figure 7: Fibre Bragg Grating The size of the patches has been speci昀椀ed to give a large enough area to securely bond to the mechanical sail surface, whilst minimising the surface area that requires preparation. This is important to ensure that the full level of strain is transferred from the mechanical sail to the FBG. Along with the size of the patch, the speci昀椀c materials and manufacturing processes used contribute to the prevention of sensor slip, sometimes experienced in other systems. The composite materials chosen work e昀昀ectively with speci昀椀c adhesives to secure the FBG within the patch and experience no de-bonding over a mechanical sail’s lifetime. Adhesives are also used during the installation process to prevent de-bonding. The preparation and installation of the Image: Interrogator unit system is not disruptive to the mechanical sail body material, so does not cause any damage to the structural integrity of the sail. Fibre-optics systems have been proven to withstand 100 – 200 million cycles of high strain loading, with such being experienced by a wind turbine over its 25-year lifetime. This improvement is largely due to its use of glass and glass composite materials during manufacture. These materials do not su昀昀er from work hardening or similar structural issues, meaning they are practically immune to fatigue and therefore failure. Image: TLI unit 16
THE CRITICAL ROLE OF ACCURATE WIND MEASUREMENT FOR WIND ASSISTED SHIP PROPULSION Fibre-optics does not require an electrical connection to the sensors themselves, instead just requiring power to the interrogator. This means it is both immune to lightning and EMI interference, resulting in a low noise system and therefore more accurate data. In adverse weather conditions, as it could occur on board a seagoing ship, the system can remain operational, generating the con昀椀dence and reliability needed. This is important when used in conjunction with control algorithms for the implementation of the mechanical sail wind orientation or adjustment parameters, such as Angle of Attack to the incoming wind for a Wing Sail or change of RPM in case of Rotor Sails. Strain Sensor FBG Temperature compensation sensor Fibre-optic cable Transmitted light (96%) STRAIN STRAIN A small amount of light (4%) is re昀氀ected from each FBG sensor Figure 7: Sensor patch (left) and Fibre Bragg grating structure during strain load 17
THE CRITICAL ROLE OF ACCURATE WIND MEASUREMENT FOR WIND ASSISTED SHIP PROPULSION IMPACT ON SHIP PERFORMANCE These pages illustrate through a typical mechanical sail arrangement example, how Insensys 昀椀bre-optics sensors can identify accurately the locally developed thrust forces and how the system can help to adjust the mechanical sails operational parameters (RPM, AoA, etc) so that thrust generation and hence WASP performance is largely improved. In the below graphic example (Figure 10) taken from the academic literature[8], a typical oil tanker ship is installed with four (4) 30x5 meter (height x diameter) rotor sails. A ship speed of 12 knots, true wind angle (TWA) of 650 and true wind speed (TWS) of 12 m/sec (23.5 knots) is taken as calculation base. The graphic shows a visualisation of the locally incoming wind conditions to each rotor sail (apparent wind direction and apparent wind speed) compared to the Anemometer readings (as received from the bridge location, here at AWA=42.10 and AWS=16.1 m/sec) and potentially a LIDAR reading installed in the forecastle such as to measure the undisturbed homogenous 昀氀ow forward to the ship (AWA 450, AWS = 16.5 m/sec). The locally incoming wind conditions to each rotor sail are calculated as per the suggested valid aerodynamic interaction e昀昀ects method described. It is evident that each of the installed Rotor sails operate under di昀昀erent incoming wind conditions compared to the theoretical Anemometer and LIDAR readings, with the LIDAR reading being more reliable as an incoming undisturbed apparent wind condition measurement. For the sake of providing certain comparative performance results of the potential gains from such a con昀椀guration, if the four Rotor Sails are installed with Insensys 昀椀bre-optics sensors, we consider a Lift coe昀케cient range of 9-9.5 and Drag coe昀케cient range of 2.5-3 for each Rotor Sail at a max RPM of 180 which provides for a velocity ratio range of 2.6 – 3.1. Figure 10: Arrangement of four (4) rotor sails on a tanker ship with respective incoming apparent wind conditions[8] (Source: Wind Propulsion Principles, Konstantinos Fakiolas, Edition 3) Expected Fwd Thrust Real Fwd Thrust force Performance force (kN) (kN) Di昀昀erence Anemometer-based Insensys-detected Rotor Sail No 1 100.98 120.33 19.16% Rotor Sail No 2 100.98 91.34 -9.5% Rotor Sail No 3 100.98 90.96 -9.92% Rotor Sail No 4 100.98 117.29 16.15% 18
THE CRITICAL ROLE OF ACCURATE WIND MEASUREMENT FOR WIND ASSISTED SHIP PROPULSION 4.13% improvement in WASP performance with Insensys Save over $100,000 per year Based on sailing 24 hours per day for 180 days per year It is evident that the forward installed Rotor Sails (No 1 & 4) can perform better compared to the Anemometer outputs, since they encounter more undisturbed 昀氀ow while the aft located Rotor Sails No 2 & 3 receive more disturbed 昀氀ow from both the ship and the forward located Rotor Sails. Under the co-ordinated operational parametrisation as detected and enabled through an Insensys 昀椀bre-optics system, the four rotor sails will overall perform better by 15.47% than anemometer-measured in such instant wind conditions, while operational adjustments can be made for the detected under performing Rotor Sails to further improve their performance on basis of the real local incoming wind conditions – if such can be feasible. For example, Rotor Sail No 2 is supposed to encounter an apparent wind of 42.10, however, in reality, the encountered wind is more close-hauled to the bow at 37.60, hence prompting for a higher RPM setting which could inadvertently give a larger side force than expected or consume more electrical power than needed. The 昀椀tted Insensys sensors in the above cases would reveal the real forward thrust force experienced by each Rotor Sail and the control logic of the Rotor Sails would conclude that their performance is not matching the one anticipated from the anemometer reading, thus adjusting to a better total forward thrust performance setting (i.e. in this case through RPM adjustments). The added value of 昀椀ne-tuning such operational parameters as enabled through the Insensys 昀椀bre-optics sensors can be re昀氀ected in the below total Voyage cost savings for the given ship (assuming a constant sailing speed of 12 knots, main engine propulsion power of 7 000 kW, speci昀椀c fuel oil consumption 170 gr/kWhr, propulsion e昀케ciency of 0.7, marine diesel oil fuel price of 700 usd/ton, CO2 cost of 100 usd/tonCO2, MDO carbon factor 3.2): Propulsion M/E power (%) Fuel savings CO2 savings Total Voyage cost power (ton/hr) (tonCO2/hr) savings (USD/hr) Without WASP 100 - - - With WASP 49.12 0.605 1.936 617.1 With Insensys 642.6 昀椀tted WASP 47.1 0.630 2.016 (+4.13%) It can be clearly seen that there is a 4.13% instant boosting of the voyage pro昀椀tability from a WASP system operating under such incoming wind conditions, when Insensys 昀椀bre-optics sensors are 昀椀tted. In the case of Rotor Sails, such RPM adjustments not only improve the forward thrust bene昀椀t for the ship hence the propulsion power replacement and fuel savings, as demonstrated), but also improve the power consumption pro昀椀le of the Rotor Sails, hence can also contribute to auxiliary genset fuel consumption saving. Such performance bene昀椀ts also apply to Wing Sails supporting more accurate Angle of Attack adjustments to enhance total forward thrust force, and for Suction wings for optimal AoA and suction power adjustments. 19
THE CRITICAL ROLE OF ACCURATE WIND MEASUREMENT FOR WIND ASSISTED SHIP PROPULSION BENEFITS OF LOAD & STRESS MONITORING Another signi昀椀cant advantage provided by the Insensys 昀椀bre-optics sensor system is that the local loads and forces measured can provide valuable real-time information about the developed stresses and the fatigue pro昀椀le of the mechanical sails. All mechanical sail types will be called to operate in a fully dynamic and variable loading stress environment, while at the same time pressures for cost e昀케ciencies will require the optimisation of structures, both the masts and the foundations. Accurately monitoring the load variations will help to early detect fatigue problems but also understand the full-scale maximum loads encountered during WASP sailing at real seas, hence providing a cut-o昀昀 or protective positioning of the mechanical sails as well when such critical conditions happen. Insensys 昀椀bre-optics sensor systems have been installed since 2006 in all the masts of the sailing superyachts Maltese Falcon (88m) and later Black Pearl (106m) in 2016, where a DynaRig[9] sail system is 昀椀tted for delivering wind propulsion, with these ships having logged to-date in excess of 250,000 sea miles, with most voyages spending 80% of the time under sail power alone. During an extreme event which occurred while sailing in violent Storm (Beaufort scale 11), the Insensys 昀椀bre- optics sensor system was able to identify and analyse the threatening situation. The vessel, with heavily reduced sail, was rolling in a big sea state between 10 and 26 degrees in a 9 second period, as can be seen in the heel data (Figure 11). This rolling contributed statically and dynamically to the mast loads by increasing them. The crew had previously reduced sail in the correct sequence and correctly altered the trim angle in response. The collected data was later able to be used for further crew training and to validate predicted design loads with those experienced. Most Rotor Sails and Wing Sails, where their height span exceeds the ship’s air draft are using tilting mechanisms, but not dimensioned structurally to be lowered during heavy weather conditions, because otherwise the structural reinforcement required for the foundation and hinge mechanism would be very considerable, thus increasing the costs and structural fatigue. Hence WASP system manufacturers recommend that when heavy weather conditions appear (i.e. rough winds during storms) the mechanical sails should remain upright or partially reefed, however the load stressing remains, the magnitude of which would be important to always know and record. In addition, such stress monitoring can be a useful tool for WASP technology providers to optimise further their own structural designs or even prove to ship owners and operators that their major Figure 11 :Data logging from Insensys 昀椀bre-optic sensors showing the combined components are durable and require less maintenance, a competitive advantage in bending and torque percentage – top chart – versus wind speed, mast angle and heel angle (following charts). a growing WASP vendor market. (Courtesy of Southern Spars, https://southernspars.com/dynarig/ 20
THE CRITICAL ROLE OF ACCURATE WIND MEASUREMENT FOR WIND ASSISTED SHIP PROPULSION 21
THE CRITICAL ROLE OF ACCURATE WIND MEASUREMENT FOR WIND ASSISTED SHIP PROPULSION Figure 12: Real time load and driving force read outs (basis bending and torque loads) used by the crew to ensure the vessel is being operated safely and to optimise performance, as derived from the Insensys 昀椀bre-optics load monitoring data. Figure 13: Long term structural health and design endorsement plots of polar loads on deck bearings, derived from composite strain measurements in the rig. Courtesy of Southern Spars, https://southernspars.com/dynarig/) 22
THE CRITICAL ROLE OF ACCURATE WIND MEASUREMENT FOR WIND ASSISTED SHIP PROPULSION TRANSLATING DATA INTO PERFORMANCE The Insensys 昀椀bre-optics system provides for a direct thrust measurement system so that the forces developed from each mechanical sail can directly be compared with the aerodynamic performance curves, hence proving the performance expectations, and avoiding costly disputes during ship delivery. As shown in 昀椀gure 12, with the Insensys 昀椀bre-optics sensors installed in every and each mechanical sail unit on board a ship, the load sensing data can be utilised for multiple operational optimisation actions: • Adjust each individual mechanical sail operational setting (RPM, AoA, etc); • Understand the dynamically developed forward and side forces during the dynamic operating environment (i.e. ship motions, gusty winds, etc); and • Apply safety restrictions of the WASP system parametrisation e昀昀ectively and real-time, to avoid conditions of excess side forces, excess heel, or excess structural & dynamic loading to the sails. Such accuracy of measurements takes much more importance when the ship attempts to perform wind and weather routing optimisation, since the selection criteria of each course and speed adjustment during this route optimisation depends on comparing the weather forecast with the actual incoming winds locally on the ship and on each of the mechanical sails. In addition, another very valuable use of the Insensys 昀椀bre-optics sensors is to provide a reliable and accurate means to con昀椀rm the performance of each mechanical sail which secures contractual obligations between WASP vendors and the purchasing party (ship owner or shipyard) during commissioning and sea trials. Because of the complex operating environment on a ship, it is very risky for WASP technology providers to commit to contractual performance 昀椀gures not directly related to the force development capabilities of the mechanical sails as designed, tested and certi昀椀ed. Insensys was founded in 2002 with the purpose to design and install a 昀椀bre-optics load measurement system into the carbon 昀椀bre DynaRig masts of the super yacht, the Maltese Falcon. These sensors (around 36 sensors per mast) continually measure and log the strain across the entire rig, displaying the load data in real time for the Rig Master to control all 3 masts almost single-handedly, thus enabling the yacht to sail so safe and e昀케ciently, that it can theoretically make it round the world without using fuel. The FBG sensors as presented above are located, and aligned so that bending loads in both planes at various points up the rig and torsional loads can be monitored and recorded. (Figure 13) An individual voyage can be analysed for future route optimisation, as well as 5 years of data being compiled for analysis rather than yacht/mast visual inspection, saving signi昀椀cant costs and time out of the water and providing additional assurance to insurance providers thus potentially reducing premiums. Insensys sensing systems are a proven technology for wind-assisted and fully wind-powered ships providing one of the most accurate means for optimal performance in all operating conditions of the ship, whilst supporting the lifetime integrity of the wind propulsion systems by further enhancing safety and reducing maintenance costs. 23
THE CRITICAL ROLE OF ACCURATE WIND MEASUREMENT FOR WIND ASSISTED SHIP PROPULSION 24
THE CRITICAL ROLE OF ACCURATE WIND MEASUREMENT FOR WIND ASSISTED SHIP PROPULSION ABOUT THIS WHITE PAPER AUTHORS Konstantinos Fakiolas is a Naval Architect & Marine engineer with over 20 years of 昀椀eld experience in energy e昀케ciency application and environmental technologies adaptation in modern ship design and shipbuilding. Since 2014 he has been specialising in Wind-Assisted ship propulsion by engaging with the very 昀椀rst commercial WASP ship Integration projects, participating in research, supporting WASP technology providers product development and implementing WASP project management in newbuilding and retro昀椀ts. He is the Author of the 昀椀rst global maritime industry technical publication about Wind Propulsion, the ‘Wind Propulsion Principles’ issued since May 2020, which is a complete guide to ship owners, operators, designers and shipyards for WASP ship applications. Insensys is a fast-growing British success story in 昀椀bre-optics sensing technologies. Founded more than 20 years ago as a manufacturer of smart carbon 昀椀bre super yacht masts, and over the following 5’ years we evolved to focus on our core business: Fibre-optics sensing technology for wind turbine control. As the core business continues to grow, we have also continued our diversi昀椀cation into other renewable energy markets using our innovative sensing solutions. Insensys have broadened it’s specialist optics system product portfolio, and now have o昀昀erings and scale of business to satisfy a range of demands. Insensys has proven solutions and capabilities to deliver optimal sensing systems to a wide range of applications most notably in the wind energy and marine sectors. REFERENCES [1] FuelEU Maritime initiative: Provisional agreement to decarbonise the maritime sector - Consilium (europa.eu) [2] Guidelines on life cycle GHG intensity of marine fuels (LCA Guidelines) (imo.org) [3] SkySails GmbH - WESSELS (archive.org) [4] E-Ship 1 - Wikipedia [5] Wind Scan JIP: Wind assist in Operation, Gijs Struijk, MARIN [6] Norsepower Rotor Sails con昀椀rmed savings of 8.2 % fuel and associated CO2 in Maersk Pelican project — Maersk Tankers [7] Wind Propulsion Principles – The Book, Edition 4, Konstantinos Fakiolas [8] [8] Design, Operation and analysis of wind-assisted cargo ships, Fabian Tillig, Jonas W. Ringsberg [9] DynaRig - Southern Spars 25
THE CRITICAL ROLE OF ACCURATE WIND MEASUREMENT FOR WIND ASSISTED SHIP PROPULSION Sensing for a better world INSERT TITLE 26