THE CRITICAL ROLE OF ACCURATE WIND MEASUREMENT FOR WIND ASSISTED SHIP PROPULSION ELECTRICAL RESISTIVE STRAIN GAUGES STRAIN GAUGES Complexity of Installation Calibration requirements Susceptibility to motions Total life cycle cost Accuracy A more localised approach for receiving direct thrust measurements of the wind propulsion unit is to install typical/electrical resistive strain gauges, either on the lower body of the mast or on the foundation structure. Strain gauges are sensors whose electrical resistance varies with the applied force (strain, tensile and compressive) thus it can be used to measure and analyse the forces and moments acting in all three axes (x, y, z) – either those coming from pressure, movements, heat and even structural changes to the material they are attached upon. When external forces are applied to a stationary object, stress and strain are the result, with stress de昀椀ned as the object’s internal resisting forces, and strain is de昀椀ned as the displacement and deformation that occur. In the very 昀椀rst recent mechanical sail applications for wind propulsion such simple mechanical type strain gauges were installed to measure the direct thrust development from the Sail and associate it with the incoming wind measurements, as validation of their performance[6], such as for example used in the ex- ‘MAERSK PELICAN’ Aframax Tanker installation during 2019, where two (2) Rotor Sails were 昀椀tted. The strain gauges were located on the foundation of the Rotor Sail, as it is the anticipated that the developed aerodynamic forces from the sail will be transferred to the supporting structure and then delivered through that to the ship’s structure. Alternatively, the industry-wide strain gauges can be used and have been actually installed in the very 昀椀rst mechanical sail applications due to their relatively low cost of manufacture and simple installation onto metallic surfaces. However, strain gauges are manufactured from metallic materials that do not possess desirable properties for repetitive, high strain loading, where degradation and fatigue can occur prematurely when subject to these conditions, making them unsuitable for use some applications. One of these applications is the Wind Energy market, previous testing shows that strain gauges fail at around the six-month mark, or at approximately 3,000 cycles of high strain loading, when installed in a turbine – hence it is expected that the dynamic fatigue and multiple loading environment on a ship at seas will provide even worse performance. Electrical strain gauge systems measure the change in resistance at each point and therefore require power supplied to all sensors. In certain applications, such as those working closely with volatile or 昀氀ammable materials, as for example on deck mounted mechanical sails of Oil/Product tankers and Gas carriers, this is certainly a safety concern. Another worrying issue is that electrical strain gauges are prone to becoming detached from the object’s surface, due to the installation issues experienced with many materials, and as a result, it is likely that the strain gauge produces inaccurate data, as the strain transfer between the materials is weakened. There are also other issues related to strain gauges’ operational and measurement reliability especially when considering frequent calibration needs, being susceptible to electromagnetic interference, humidity, creep and fatigue, factors which render their long-term reliability unsuitable for mechanical sails. 11
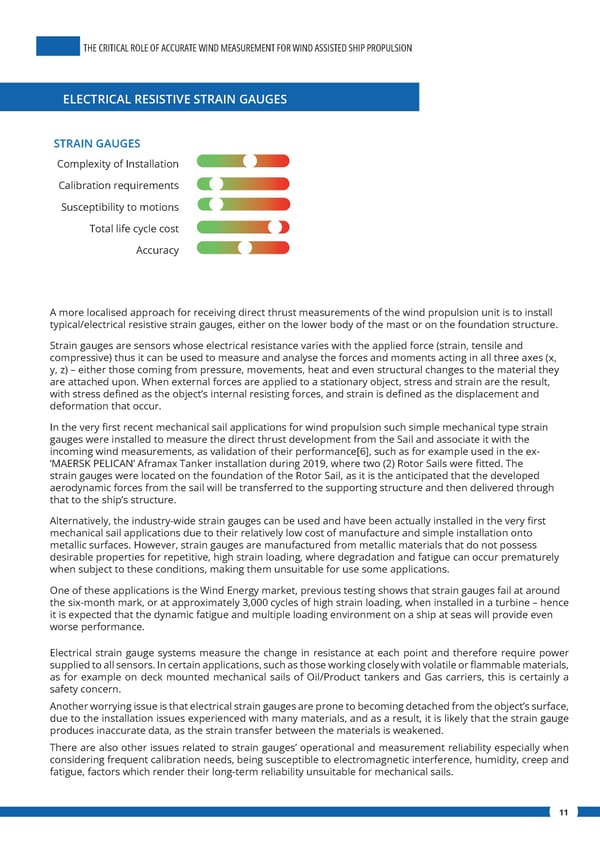