THE CRITICAL ROLE OF ACCURATE WIND MEASUREMENT FOR WIND ASSISTED SHIP PROPULSION ACCURATE FIBRE-OPTIC WIND SENSING METHODS FIBRE-OPTICS Complexity of Installation Calibration requirements Susceptibility to motions Total life cycle cost Accuracy Considering the above currently used options, the noticed limitations, restrictions and impact on delivering the maximum possible inherent performance capabilities of mechanical sails, Insensys 昀椀bre-optics sensors present a more reliable and enhanced alternative as a WASP wind and load sensing measurement solution. Fibre-optics sensors have long been used in land-based wind turbines, and have been proven very reliable, having as prime purpose to measure the wind turbine blade root bending moments for active control of wind turbine generators, by dynamically adjusting the pitch of each turbine blade in real time, thus increasing the wind turbine reliability and e昀케ciency. Insensys sensors are currently installed (with a reference base of > 7,000 systems) in composite 昀椀bre blades over 100 meters long, to continually measure the bending moment and loads at the root section of the blade where it connects to the rotor. Each blade load is balanced by making small pitch adjustments to each blade, enabling it to capture more or shed wind load accordingly. This enables the turbine to perform better (generating more electrical power), as well as reducing fatigue and maintenance on key drive train components. This application is called IPC (Individual Pitch Control). IPC delivers that extra 10% percent of turbine performance, similar to a turbo in a combustion engine. Equivalently, when a similar Insensys 昀椀bre-optics sensor system is used in mechanical sail applications for ship wind propulsion, they can provide multiple load point measurements, which can serve below purposes: • Depict at any given point of time the actual localised forces developed across the mechanical sail height (wind induced and ship induced), • Support accurate adjustments of the mechanical sail operating parameters (i.e. Angle of Attack, RPM, etc) for real-time optimal performance, • Compare with surrounding principal ship wind sensing system (i.e. anemometers and/or LIDAR), • Detect fatigue load limits and provide feedback on structural health of the mechanical sails, • Alert on-time for possible excess forces developed to the mechanical sail, undesired by means of ship safety. Insensys have proven wind load control systems for WASP technologies 昀椀rst trialled on DynaRig structures in 2002, which, similar to the IPC application for wind turbines, can provide advanced control loops to optimise their wind capture. Optical sensors embedded into the WASP structures can provide a real time control loop to adjust the structure, either in pitch, shape, or pro昀椀le. In a typical wind propulsion system arrangement (i.e. for a Wing Sail, Suction Wing, Rotor Sail, etc) a number of optical sensor arrays are installed in carefully selected locations usually where they experience a signi昀椀cant magnitude of strain signal, thus mostly near the bottom part of the Sail mast or tower and in other locations of critical importance, connected through Optical 昀椀bre Kevlar-reinforced cables to the Interrogator unit installed locally or remotely within the control panel of the wind propulsion system as seen in 昀椀gure 9. 14
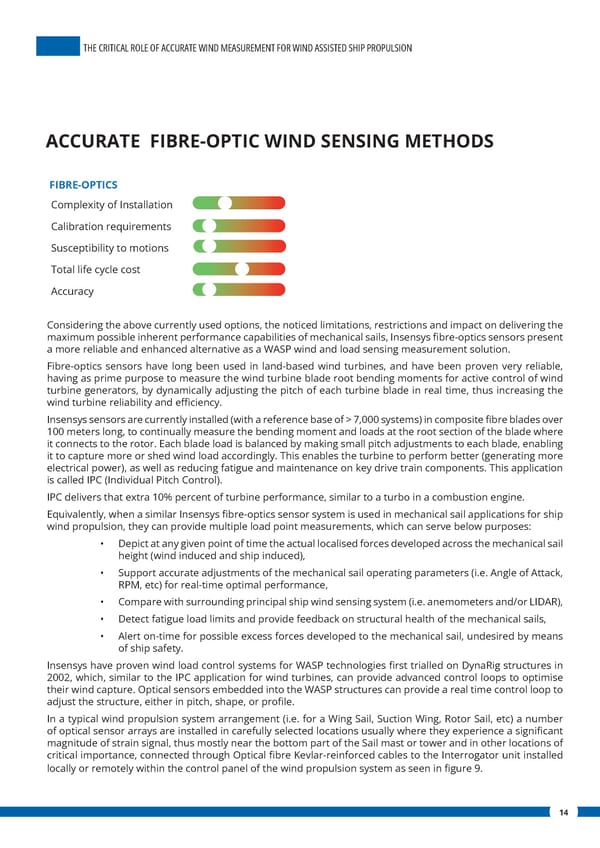